A combination that shows you care: ISO certification and workplace safety
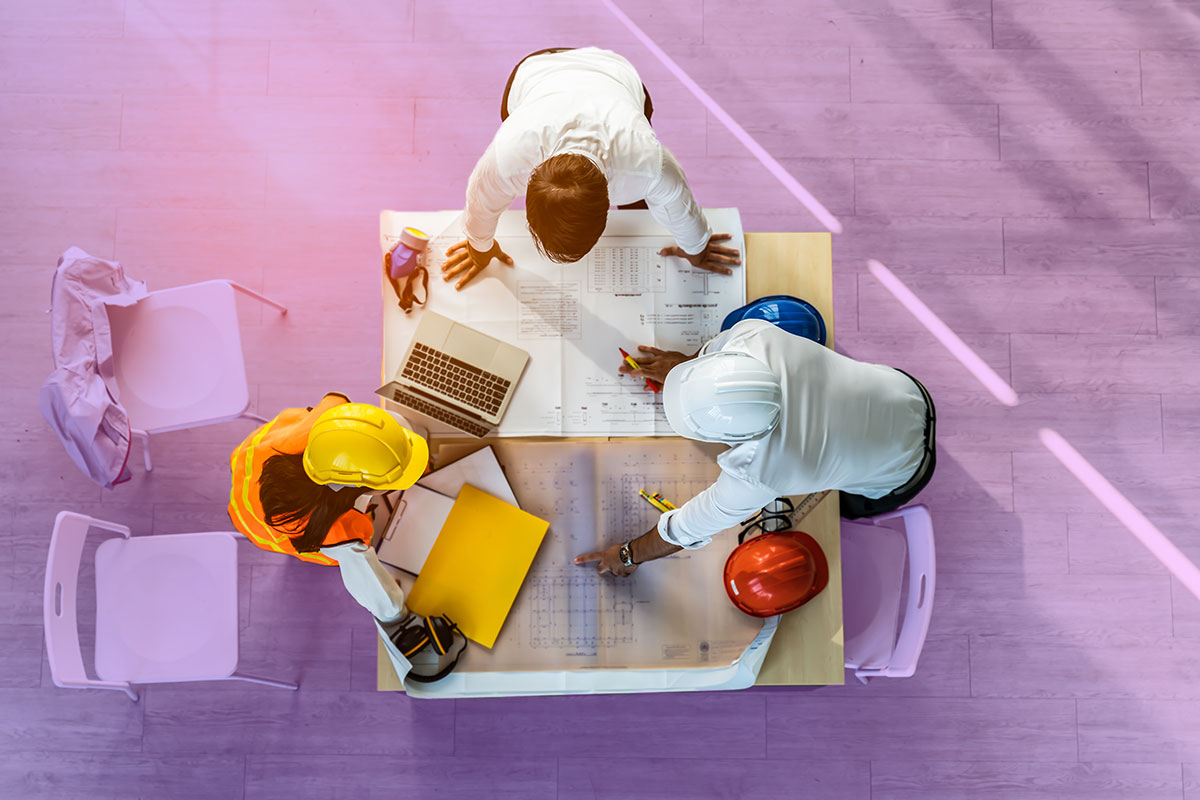
27 February 2024
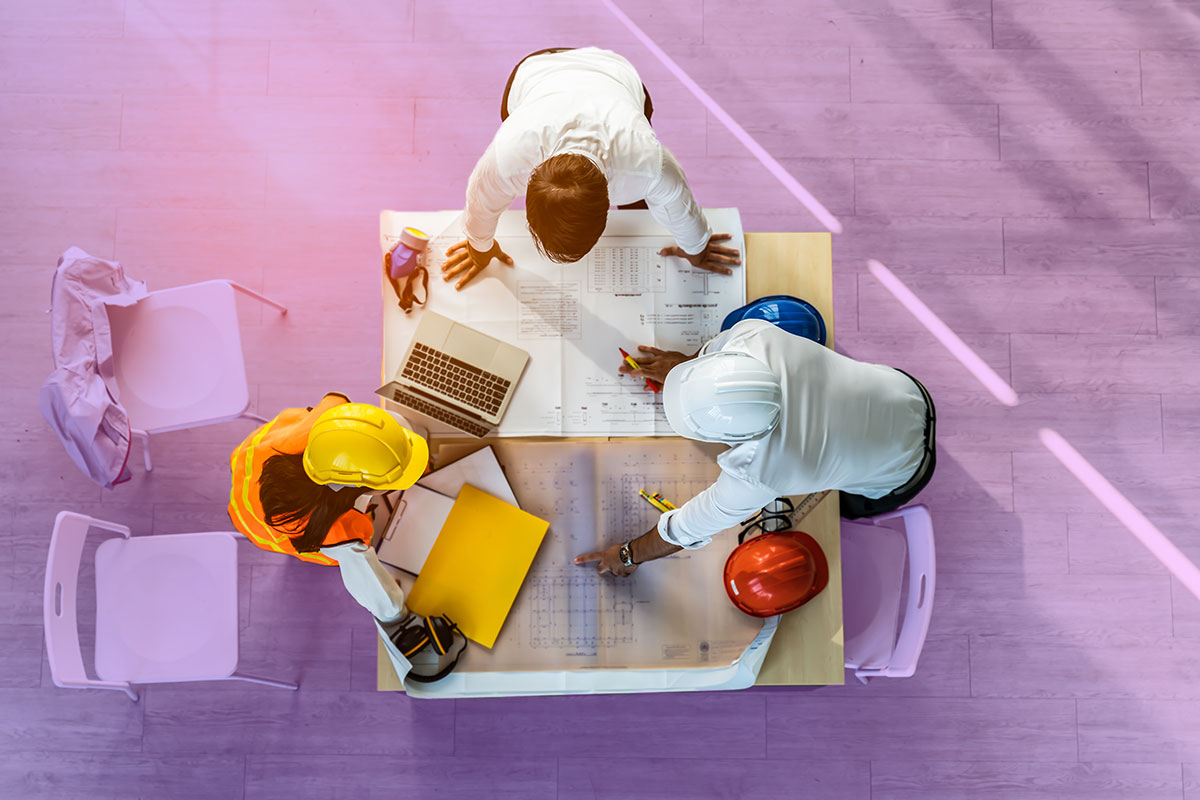
The introduction of stringent – and complex – industrial manslaughter laws across Australian states has helped send a strong message to businesses that workplace safety is paramount, and every employer must ensure they’re not only promoting safe working practices, but they are also taking active measures to eliminate, reduce, and rectify any risks.
And while our stringent safety laws are designed to protect people, some Aussie workplaces are simply not listening; according to insights from Safe Work Australia, in 2022, there were 195 worker fatalities due to traumatic injuries sustained in the course of a work‑related activity. And although stats show a 30 per cent decrease in fatalities since 2012, the numbers are still confronting:
- 93 per cent of all fatalities were male.
- Workers aged 45 and over accounted for 62 per cent of all workplace fatalities recorded.
- Younger workers aged under 25 years old had the lowest fatality rate.
- NSW had the highest number of workplace deaths with 50 followed by Queensland and Victoria recording 49 and 40 respectively.
Australia has some of the most complex Work Health and Safety (WHS) laws in the world, and even with all this, there’s still an obvious need to make workplaces even safer places for workers. With effective processes in place, incidents, injuries, and accidents can be prevented – and that’s where ISO Certification can help.
What’s certification got to do with it? ISO 45001 sets the safety standards for workplaces to achieve and maintain.
ISO 45001 is a globally recognised Occupational Health and Safety Management System that helps organisations proactively manage workplace safety, prevent work-related injuries and illnesses, and promote a culture of safety within the workplace. This certification is fundamentally designed to reduce workplace fatalities and disease through the implementation of robust safety management systems. Achieving ISO 45001 certification is best done through a Plan-Do-Check-Act model, and this is offered by our team of specialists at Citation Certification.
The Plan-Do-Check-Act model allows businesses to quickly and easily review their WHS management system, monitor its effectiveness, identify potential gaps in the system, and provide new opportunities for improvement.
Regular audits using the Plan-Do-Act-Check model can help reduce work-related incidents both on and off-site. This can have a positive impact on workplace safety, productivity, team morale, and more.
3 ways ISO 45001 can improve safety in your workplace:
1. Proactively identify, assess, and address hazards in the workplace
Think of the Plan-Do-Check-Act framework as an early warning system for potential risks, so you can prevent accidents rather than react to them.
The Plan-Do-Check-Act model means you will be able to identify potential hazards in the workplace and create firm processes to minimise the risk of injuries, illness, and deaths on or offsite.
Achieving ISO45001 should mean these benefits for your business:
- A sense of trust between employer and employees.
- A safer, happier workplace.
- A positive reputation with third parties (increasing potential tender prospects).
- Lower insurance premiums.
- Reduced employee turnover.
2. Minimise risks with continual analysis and improvements
Identification of WHS risks and opportunities is the first step in the process. The next step is to analyse the associated impacts to identify and take appropriate actions to minimise risks, eliminate hazards or correct gaps in the system. Like all ISO standards, ISO 45001 is about continual analysis and improvement.
Addressing the “check” and “act” stages of the Plan-Do-Check-Act model can further minimise risks and make your workplace a safer, more efficient space. Here are some potential questions you and your team can cover during the review or analysis stage:
- Have there been any unexpected challenges within the business recently?
- Have any of our team members reported challenges or accidents on or offsite?
- Have we been using any new machinery that could be hazardous?
- Are our team members trained well enough to use this machinery safely?
- Have we been working on any new or challenging sites recently?
Getting audited towards ISO45001 will encourage your business to review its WHS system and processes quarterly, bi-annually, or annually to keep on top of process improvements and workplace safety.
3. Implementation of processes to help reduce the risk of injuries and illnesses
As your WHS system and processes improve, your team members will require additional training to get up to speed. This training will not only improve your team’s skill set, but their new and improved knowledge will allow them to work safer on and offsite. Thanks to improved processes and training, your team members will feel more confident in their roles, be more mindful of best practices and take responsibility for the safety of themselves and co-workers.
Your journey to obtaining ISO 45001
Let’s start at the beginning: to achieve ISO 45001 certification, you need to prove compliance with the requirements of the Standard. This requires:
- Passing an assessment, that can be conducted by Citation Certification.
- Implementing any necessary improvements to better safety in the workplace.
Interested in learning more about ISO 45001 and how it can help your business? Reach out to the certification specialists at Citation Certification today for a no-obligation, confidential chat.